Stamping Presses
DREHER Automation perfect your punching process
The production of complex sheet metal components requires a series of operations. In this context, the use of progressive dies can be the right approach for the efficient and cost-effective production of large quantities. This is one of the reasons why stamping presses, a combination of coil processing line, progressive die and stamping press, are a classic setup in a press shop.
Whether for furniture fittings or larger body parts in the automotive industry, we work together with you to develop your perfect systems solution for your stamping process. The degree of automation of the entire forming line is tailored to your requirements and we select the optimum straightening technology for your materials.
From the Progressive Die to the conclusive overall Concept - DREHER Automation is your competent Partner
Progressive dies are used for example in the automotive, electrical, furniture and domestic appliance industries. They are used when the cost of sheet metal parts needs to be kept to a minimum for high volume production. The decision as to whether a part can be produced with a progressive die or a transfer tool usually depends on the size and complexity of the sheet metal part and the planned production volume. This process is particularly suitable where large deep drawing operations are not required.
A progressive die usually consists of several tool stations. In each tool station one or more forming operations (e.g. stamping, drawing, bending, embossing, punching, cutting) are performed in sequence. The sequential stages of the sheet metal parts are held by a carrier strip during transport through the forming operations. The sequential part stages are not separated from the carrier strip until the final station.
Which type of forming press is suitable for the stamping line depends largely on your forming process. Eccentric presses, toggle presses, or servo presses are all possible. Of course, we will be happy to assist you in choosing the right type of forming press.
In progressive die applications, the material is always supplied from a coil. The coil straightener then equalizes the coil curvature of the sheet metal strip before the sheet metal strip is fed precisely into the actual forming process by means of a coil feeder. To achieve the best possible part quality, a optimal strip side guidance throughout the entire forming process plays a central role. The coil feeder must also be able to give the strip enough space to flow during the forming process by using a cycle ventilation. The finished part can then be discharged either via a finished parts conveyor or another end-of-line solution.
Do you have limited experience in metal forming technology or are you interested in implementing a new forming process in your press shop? We will advise you during the planning phase with the help of our professional project management team and put you in contact with other reliable partners (e.g., press manufacturers, tool manufacturers). Afterwards, we support you throughout the implementation process until the new forming process is running smoothly in your press shop. For us, this includes not only professional production support, but also, for example, CE marking.
Increased Efficiency with an integrated Control Concept for your Stamping Press
Our control concept, developed together with Siemens, completes your comprehensive concept across all system components (coil processing line, progressive die, and stamping press). Our S7 controll system with Safety Integrated (Performance Level d) is not only compatible with any press control system. We can also take care of the press control, for example as part of a press retrofit of an existing stamping press.
We at DREHER Automation also value the productivity-enhancing benefits of user-friendly and self-explanatory operation and visualization. For this reason, our visualization is not only carried out on large touch panels at a central location via WinnCC (TIA portal), we are also happy to develop for you an unique visualization concept for the entire stamping line. Synoptics for automatic operation and sequence synoptics for coil and tool changes are mandatory for all our customers.
Press Automation from DREHER Automation is renowned in the megal forming industry for their longevity. This is also guaranteed by our excellent After Sales Service. For just-in-time support, all our systems are equipped with remote maintenance access.
Your Contact Partner
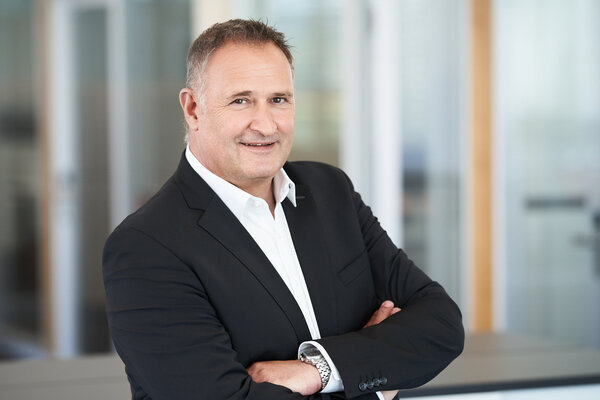
Claus Dratz
Director Sales Southern Europe & Mexico
Your direct line to DREHER Automation
Do you have any questions or would you like us to advise you? Simply fill out our contact form. We look forward to hearing from you.